Supply Chain Overdue, Construction, & COVID-19
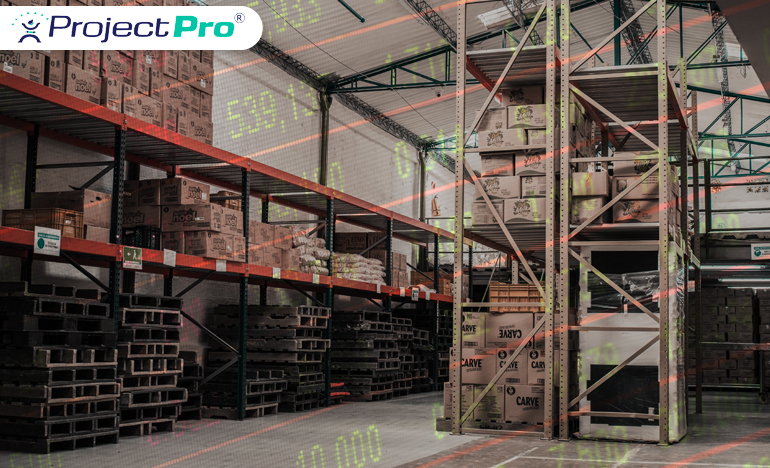
The Expected Price Rise for Materials and Strategies to Sustain
The year 2020 has been an unfavorable year for the construction industry. The spread of the global pandemic has led to massive loss of jobs, suspensions, and termination of project contracts. Amidst this entire crisis, one thing that has become a major concern for contractors is the sudden rise of the material prices. Though the reports from the beginning of 2020 already shared the expected rise in prices, COVID-19 has played a significant role in extended uncertainty. Therefore, the consideration that the downfalls in the supply curve could be a large factor that may affect the construction companies in 2020 along with sudden price increase.
Digging into the detail…
Most construction companies based in the US are dependent on China for 80 percent of their construction supplies. However, the shutdown after the outbreak of coronavirus in Wuhan, China has resulted in slowed manufacturing and delayed exports. Even if the manufacturing process in China resumes to pre-COVID normal output and all economic functions have resumed, the time it will take to recommence supply chain activities is still unpredictable. For construction project managers and contractors who understand the concept of the supply-demand curve, COVID-19 will lead to a shift to the left, resulting in increased prices with demand standing still. Though the orders of Federal and State authorities have restricted construction not defined in the essential services category, the phased opening has again made the demand to rise. Even the safety guidelines such as reduced workforce or social distancing at the site have not made the demand decrease. Since a single case of infection at the site could delay the entire contract, the government has defined certain limitations and guidelines in order to open the construction sites. This could simply be understood as uncertainty with the project deliveries, as the demand and supply curve is unstable. All these varying situations signal a gradual increase in the prices for the material and all this requires extreme tracking of the supply chain with the help of accounting software for subcontractors. Moreover, when a big portion of the construction material supply awaits from China’s end, it would not be easy to predict the status of the construction industry in the United States. As a result of unpredictable situations, the likeliness to reduced cash flow will increase which would ultimately cause inflation in the market.
What must be the Strategy Contractors Need to Adopt?
In times like these, communication is the key. The construction companies that tend to have better relationships with the project owners and suppliers could work on supplies as well as schedules. In simple words, considering the “what if” factor should be the priority when delays/restrictions to the projects are expected. This needs immediate evaluation of jobs that can be carried using the least amount of resources while ensuring payments are made to the suppliers. Also, the inflation that is followed by the restrictions on supplies can be controlled by interacting with multiple contractors for a price that is mutually agreed upon. Moreover, any liabilities on the supply or issues which supplier is having with the material should be considered to ensure a consistent supply during the downtime. If you had a conservative approach to the supply chain, make sure you make new contacts during the pandemic and diversify for improved material availability at discounted prices. Also, the track of supplies must be kept using a Microsoft Dynamics accounting software that can help streamline the material availability at site.
Baking Plans for Future
When planning to sustain your business and navigating through COVID-19, make sure you always have a watch over supplies and the costs involved. Your future plans should have space for the expected inflation in the market so that an improved budget allocation could be done. Moreover, any bids related to construction supplies should include the expected price rise factor to avoid sudden fluctuation in the budget. Also, to avoid any implications in the future, contractors should try to understand the need for change with the contracts for future projects to avoid any liabilities related to delayed deliveries under COVID-19 restrictions.