Top 7 COVID-19 Related Construction Challenges That Contractors Will Face In 2021
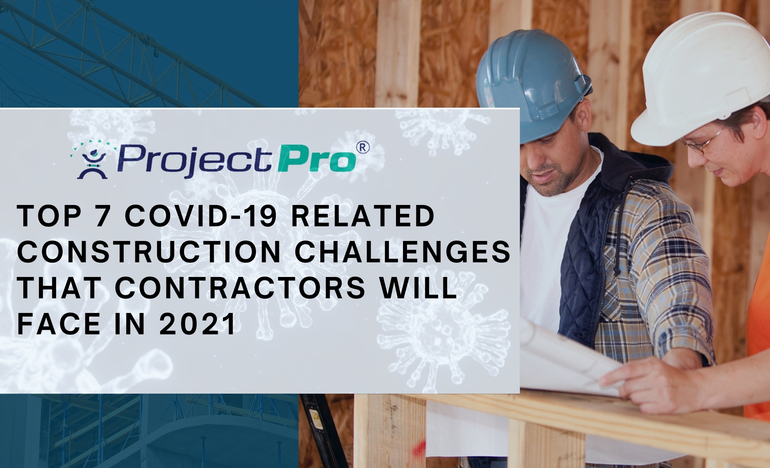
It’s been more than a year since the spread of the global pandemic beginning from Wuhan, China, in December 2019. Since it has got significant effects on the construction industry, the contractors across the globe need to deal with delays, unexpected shutdowns, labor shortage, layoffs, and of course lawsuits and financial clashes.
Even though construction was deemed as an essential business in most parts of the world including the United States, the restrictions possessed on continuing the construction work made the situation much more difficult. Especially, the loss of supply chain, lack of skilled labor, and limited workforce rules were some of the significant reasons for the downtime.
Also, large contractors who were somehow capable of continuing with their projects have to struggle to deal with unwanted expenses on safety gear such as gloves, masks, sanitizers, as well as routine cleaning of the sites.
In simple words, the entire year of 2020 happened to be a period of fluctuations and instability for the construction contractors. And even now when 2020 has ended, the effects of the pandemic are still pulling back the industry. This has made all the experts and economists predict the continuity of challenging circumstances in the construction industry during 2021.
Let us quickly begin with understanding the top 7 COVID-19 related challenges that contractors will need to deal with in 2021:
Skilled Labor Shortage
Now, this is something that the construction industry is dealing with for a long time even before the pandemic. However, the spread of coronavirus turned the situation for worse even when there was a huge shutdown of the projects. Even though many construction firms tried calling their workforce who were laid off earlier, the concerns related to family health, unemployment benefits, and job security made them refuse all such offers.
Since 2021 is seen as a year of opportunities for the construction industry, contractors may still need to deal with extensive labor gaps especially in areas with heavy construction like California, New York, and Texas. However, migration of the workers can also be a factor that might create an imbalance of resources as the maximum number of skilled laborers is likely to move to expensive markets.
Growing Backlog
According to ABC construction’s reports the construction backlog in the United States falls to 7.5 months in September 2020 which rolled down to the number after declining by 0.5 months in August and 1.5 months in comparison to 2019. This simply signified the drop in profit margins and sales in the United States with chances of an increase in the backlog in 2021.
Another thing that might leave many contractors and construction firms dishearten is the announcement made through ABC’s survey that signaled a decline in non-residential construction. All in all, the situation calls for an accelerated rise in the backlog with no signs of shrinking which might bother all the contractors irrespective of their size or area of operation.
Reduced Construction Costs
As COVID-19 has caused extensive financial loss to the existing and prospective project owners, 2021 is likely to be a year that will witness the reduced cost of construction which is something that has never happened during the past 10 years. This will not only keep contractors away from the profits but also builds the pressure of performance to avoid any delays that might add to the loss.
Meanwhile, the Turner Building Cost Index had shown a 1.5 percent quarterly reduction bringing the value down to 1171 during the third quarter of last year. As Turner Building Cost Index is the measure of costs for the U.S. non-residential construction market, it has been found to be showing the least value ever post 2010. Also, the growing competition amongst trade contractors has called for uncertainties in the market as a part of sustainability in the future.
Fewer Opportunities, Less Work
In 2021, commercial construction contractors will need to face downtime across its different sectors as the work from home scenario with restrictions on the workforce at site will continue. Even though it is predicted that the economy will rise as we recover from COVID-19, the precautionary restrictions related to health and economic circumstances can lead to unfavorable times in the matter of growth.
Also, the construction of healthcare facilities is likely to drop due to the impact created by COVID-19 making people resist physical treatment at the hospitals. And therefore, 2021 is likely to be a year focused on alternative medical care as more and more people are becoming hesitant to take their families to medical facilities.
This also calls for a decline in the development of travel, sports, and performance venues after being hit for the sales, taxes, income tolls, and other issues, that are likely to grow severe with the increasing intensity of the next wave of pandemic across global borders.
Inflation
2020 was a year full of uncertainties causing massive fluctuations with the material prices causing inflation as well as the shortage of the supply. When it was the peak of the COVID-19 in the United States, the states that considered construction as an essential business find it very difficult to get supplies even after paying high prices.
However, when the situation gets to improve post-September 2020 with resuming of projects, increasing demand for products lead to price rise in the United States, Europe, and several other parts of the world. And to avoid the situation many contractors are trying to expand their supplier network preventing price swings and avoid the effect of inflation damage the revenue and performance.
Supply Chain Issues
Even though production is back on track, the contractors are still dealing with the stress of managing the supply chain, especially the retention of material and equipment supplies. This is why contractors are aiming to build resiliency by expanding resources for the supply chains to avoid sudden cut of the supplies.
Such practices can help overcome situations where a particular supplier leave. For instance, contractors could simply approach multiple suppliers (three or up to five) preventing any halt to the supplies. Also, such tactics could help to counter the decreased shipping and air freight that caused a reduction in moving material.
Diminish State & Local Government Revenues
Last but not least, contractors in the United States are facing the challenge of retaining the revenues with state and local government projects. According to a report shared by Brookings Institution, projects lead by the government are likely to encounter a decline of $155 billion in 2020, $167 billion in 2021, and $145 billion in 2022, about 5.5%, 5.7%, and 4.7%, respectively excluding the declines in fees to hospitals and higher education.
This is happening because of the reduced funds with the government agencies that need to finance infrastructure projects like roads, bridges, and more, making many local and state agencies to look for federal funds. Also, the Industry estimates show that even with the CARE Act funds, the MTA faces at least an $8.5 billion shortfall for 2020 and 2021.
If it is something that can help contractors and construction firms get over the stress of managing supply chains, over expenses, revenue generation, project backlog, and other things, the only thing that can help save the stress is adopting the right construction accounting and project management software like ProjectPro.
To know more about how ProjectPro can help you take your business forward through the challenges possessed by the pandemic, simply reach our experts here.